Les avantages sont multiples. Sans être exhaustif, en voici quelques-uns :
La raison n°1 est probablement la facilité à produire des pièces aux formes courbes, fluides, arrondies et aérodynamiques. Aujourd’hui, le fonctionnel ne suffit plus pour vendre. L’esthétique est indispensable pour donner confiance et convaincre le client. Vous pouvez avoir la meilleure machine du marché, la voiture la plus rapide, vous ne vendrez pas si la carrosserie n’est pas de qualité. En plus, grâce à un large choix de nuances de gel Coat, toutes les déclinaisons de couleurs sont possibles. N’hésitez pas à nous soumettre vos projets, nous serons heureux de pouvoir vous accompagner dans votre étude de design avant les étapes d’industrialisation.
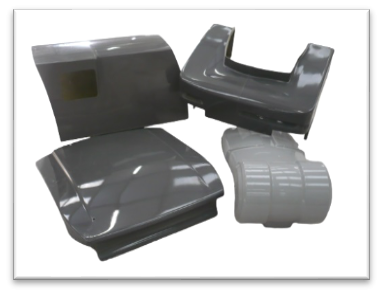
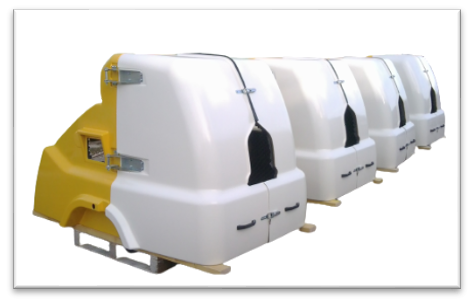
- Une autre raison importante est la possibilité de noyer dans la fibre de verre des inserts. Ceux-ci peuvent être des plaques de renfort en acier, du bois, des supports de vérin, des douilles, des écrous pour faciliter les opérations de montages/démontage. En outre, certaines zones bien précises peuvent être renforcées en ajoutant de la matière. Nous pouvons également ajouter en plus de la fibre, des tissus tressés, du kevlar…. Tout ceci permet de répondre avec précision aux contraintes fonctionnelles exigées par le cahier des charges tout en limitant le poids pièce au strict minimum.
3. Une troisième raison, qui n’est peut-être pas la plus évidente, est l’impact environnemental. Certes, le matériau composite alliant fibre de verre et résine polyester, en tant que thermodurcissable, est très difficile à recycler ou à valoriser en fin de vie. Par contre, son excellent rapport poids/résistance permet de réduire fortement la consommation des véhicules sur lesquels il est monté. En plus, notre procédé de fabrication par projection simultanée ou par moulage au contact ne nécessite pas d’énergie lors de la mise en œuvre. En effet, il n’y a ni presse, ni soudure, ni chaleur. Sur la base de son cycle de vie complet, le composite peut donc apporter une réelle solution aux enjeux environnementaux de notre époque. Il suffit pour s’en convaincre de penser à l’emploi de plus en plus présent des matériaux composites dans le transport aérien.
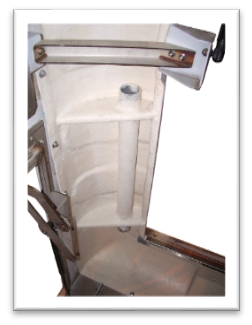
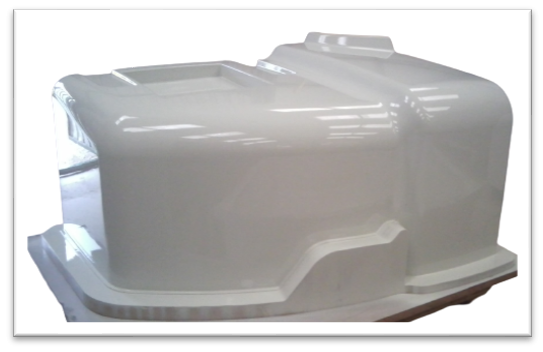
Un dernier avantage peut être cité (même s’il en existe bien d’autres) est le faible coût lié à l’investissement dans les outillages. En effet, les moules, en fibre de verre et résine, sont « tirés » directement sur un modèle en bois et mousse usiné en 3D, apprêté et laqué. Ainsi, le coût est bien moindre par rapport à des outillages usinés en acier. Le moulage au contact de pièces fibrées ou par projection simultanée est donc un procédé parfaitement adapté pour des petites et moyennes séries. Il est important pour profiter pleinement de ces avantages de faire appel à un fabricant ou sous-traitant maitrisant toute la chaine de valeur depuis le simple croquis initial jusqu’à la fabrication en série en passant par la CAO 3D, le maquettage, les outillages, les prototypes et la mise au point puis enfin l’industrialisation.